The substances in the pipelines of chemical enterprises are mainly organic chemical raw materials and products, and the waste gas pipelines in environmental protection facilities are also VOCs-related waste gas. In fact, most of the substances transported by these pipelines are VOCs! Like chemical equipment, chemical pipeline is an indispensable part of chemical production equipment, and it plays the role of connecting equipment with different process functions to complete a specific process. In some cases, the pipeline itself is also the same as chemical equipment. It can also complete some chemical processes, that is, "pipeline production". Similarly, chemical VOCs waste gas is also transported through pipelines. Often companies collect unreasonable or unsatisfactory static electricity removal measures on waste gas collection pipelines, which will lead to pipeline combustion and explosion safety accidents!
The chemical pipelines are arranged in a crisscross pattern, there are many types of pipelines, the physical and chemical properties of the conveyed medium are diverse, the pipeline system has many joints, and the incidence of fire and explosion accidents is high. The rupture and explosion accident of the pipeline is easy to expand and spread along the pipeline system, which makes the accident expand rapidly.
1. Fire and explosion caused by leakage
Most of the petrochemical pipelines transport flammable and explosive media. In fact, these substances basically belong to the category of VOCs. When the pipeline ruptures and leaks, it is very easy to cause fire and explosion accidents. This is because the leaking flammable medium can burn or explode when it encounters an ignition source. The parts where the pipeline often ruptures and leaks mainly include: the welding seam connected with the equipment; the valve sealing gasket; the reducing diameter and elbow of the pipe section; pipeline valves, flanges, and pipe sections that have been exposed to corrosive media for a long time; conveying machinery, etc. .
Leakage of pipeline quality factors, such as unreasonable design, unreasonable structure of pipeline, unreasonable connection form of pipe fittings and valves, or inconsistent thread system, without considering the problem of pipeline thermal expansion; defects in the material itself, the pipe wall is too thin, there are blisters, and the substitute material does not meet the requirements Requirements; poor processing, scratches on the inner and outer walls during cold working; poor welding quality, welding cracks, dislocation, burn-through, incomplete penetration, welding bumps and undercuts, etc.; valves, flanges, etc. Seal failure.
Leakage of pipeline process factors, such as the impact and wear of high-speed flowing medium in the pipeline; the action of repeated stress; corrosion of corrosive medium; Into the low pressure pipeline rupture, etc.
Damage caused by external factors, such as the impact of external forces such as foreign flying objects and strong winds; vibration and swaying caused by vibration and airflow pulsation of equipment and machines; damage caused by construction; earthquakes, foundation sinking, etc. Operation errors cause leakage, such as the leakage of combustible materials due to wrong operation of valves; over-temperature, over-pressure, over-speed, and over-load operation; maintenance is not, weekly, not timely maintenance, overdue and sick operation, etc.
2. Explosive mixture is formed in the pipeline
In the VOCs waste gas collection pipeline, some gases accumulate in the corners of the conveying pipeline, and flash and explode in case of static electricity! For example, the corners of the square tube are easy to make the VOCs exhaust gas accumulate in the corners of the square tube! For example, when the pipeline is stopped for maintenance and start-up, the pipeline is not replaced, or replaced with non-inert gas, or the replacement is not complete, and the air is mixed into the pipeline to form an explosive mixture; during the maintenance, the pipeline (especially the high-pressure pipeline) is not blocked and blinded. The air is mixed with the combustible gas; the negative pressure pipeline sucks air; the valve is wrongly operated, and the air leaks into the pipeline, or the combustible gas and the combustible gas are mixed, and an explosion occurs when the ignition source is encountered.
3. Overpressure explosion in the pipeline
The overpressure explosion of the pipeline is related to the operation error or abnormal reaction of the reaction vessel. The failure of the cooling medium transportation pipeline leads to insufficient or interrupted supply of the cooling medium, causing a vicious circle of overtemperature and overpressure in the production system, and eventually leading to equipment and pipelines. Overpressure explosion accident.
In the pipeline, abnormal pressure will be caused due to the polymerization or decomposition reaction. For example, in the pipeline of ethylene and peroxide catalyst, if the temperature is too high, exceeding the catalyst initiation temperature, ethylene will polymerize or decompose in the pipeline, generate high heat, increase the pressure, and cause the pipeline to burst or explode.
The pipelines that continuously discharge fluids, especially the process pipelines that discharge gaseous materials, will cause the materials in the equipment to be unable to be discharged in time due to factors such as the reduction of the conveying speed, resulting in an overpressure explosion accident of the equipment.
The material of the high-pressure system flows back into the low-pressure pipeline, causing the pressure to increase.
4. Blockage and explosion in the pipeline
The blockage of the pipeline will cause the system pressure to increase sharply, resulting in an explosion and rupture accident.
Pipelines transporting low-temperature liquids or water-containing media are prone to freezing and "freeze blocking" under low-temperature environmental conditions, especially for pipelines used intermittently. Freezing".
The pipeline that conveys powdery and granular materials with high viscosity or high humidity is easy to feed; the pipe wall adheres to the pipe wall at the corners and turns, which will eventually lead to blockage. The design or installation of the pipeline is unreasonable, such as the use of large-diameter long-distance transportation or the sudden increase of the pipeline diameter, the pipeline connection is not concentric, and it is easy to block where there are obstacles; when the material is mixed with too large fragments, it is easy to cause blockage; the material has adhesion Physical properties, if not cleaned up in time, stagnant deposits will occur, which may cause pipeline blockage.
Improper operation makes the valve in front of the pipeline not open or the valve is damaged and stuck, or the container receiving the material is full, or the flow rate is too slow, and the sudden stop will cause the material to deposit and block.
5. Spontaneous fire occurs
Coking and carbon deposits in the pipeline are easy to spontaneously ignite under high temperature and high pressure, causing combustion or explosion. Ferrous sulfide is a very common substance in the high-pressure pipelines of refineries that process sulfur-containing feedstocks. It is the product of the reaction between rust and hydrogen sulfide. When the equipment is turned off after shutdown, and when it comes into contact with air before maintenance, it will Spontaneous combustion occurs rapidly.
The temperature of the medium in the pipeline is a substance that exceeds the self-ignition point, and it will spontaneously ignite when it leaks out and comes into contact with the air.
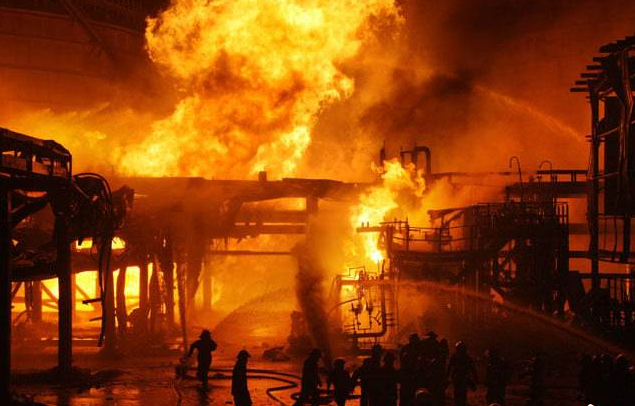
6, with a variety of ignition sources
When the material is transported in the pipeline, there are various ignition sources. When opening and closing the pipeline valve, the impact and extrusion of the valve disc and the valve seat can become the impact ignition source. When the valve is suddenly opened between the high and low pressure sections, the gas in the low pressure section is rapidly compressed and the local temperature rises, forming an adiabatic compression ignition source. In the process of high-speed flow of materials, between powder and pipe wall, between powder particles, between liquid and solid, between liquid and gas, between liquid and another immiscible liquid, between gas and a small amount of solid or liquid impurities contained in it. During the collision and friction, it is easy to bring static electricity and generate sparks.
There are various external ignition sources such as frictional impact, open flame, high temperature hot body, electric spark, lightning strike and so on around the dangerous material conveying pipeline. When the combustible material is ejected at high speed from the rupture of the pipeline or the seal is not tight, static electricity will be generated, which will become the ignition source of the leaked combustible material or the surrounding combustibles.
7. It is easy to become a channel for the spread of fire
Since the pipeline is connected to various equipment, a fire in the pipeline will not only affect the normal operation of the pipeline system, but also cause a chain reaction of the entire production system, the accident will spread and expand rapidly, especially when the medium in the pipeline is poisonous, it will be more threatening to human life. big. The explosion propagating in the pipeline will change from deflagration to detonation under certain conditions, causing serious damage to production equipment, workshops and other buildings.
Preventive Measures for Fire and Explosion Accidents of Chemical Pipelines
1. Follow the principle of safety arrangement
For transporting fire hazard of Class A and B media or toxic and corrosive media, the pipeline should not pass through buildings and structures unrelated to it. The various medium pipes that are laid on the same pipe rack must have a specified spacing. The hot material pipeline in the multi-layer pipe rack should be arranged on the uppermost layer, and the corrosive medium pipeline should be arranged on the lowest layer; flammable liquid and liquefied petroleum gas pipelines are strictly prohibited to be arranged adjacent to steam and hot material pipelines; combustion-supporting and flammable medium pipelines It is advisable to use non-combustible material pipes to separate or maintain a distance of not less than 250mm.
2. Reasonable material selection, design, processing and installation
Correctly choose the pipe material according to the properties, temperature, pressure and flow rate of the conveying medium. Do not choose any substitute material or misuse it, and do not use defective pipes. For example, when high temperature strength is required, use boiling steel and semi-killed steel below 350°C For steel, at 350°C, killed steel, molybdenum steel, Cr-Mo steel and stainless steel should be used according to different temperatures, and carbon steel should not be used; in order to prevent low-temperature brittleness, austenitic stainless steel and pipes made of aluminum and nickel-copper alloys should be used. . Supports for flammable liquid overhead pipelines shall be constructed of non-combustible materials. In order to avoid the overflow of the flammable liquid pipeline in the event of an accident, the pipeline can be laid in a trench constructed of non-combustible materials, and good natural ventilation is ensured to prevent the accumulation of flammable vapors. High temperature material pipelines should be installed with insulation layers of non-combustible materials to prevent combustibles from contacting high temperature pipelines and catching fire.
Strictly follow the design requirements of the process design, the design value of the pipe diameter should be as large as possible, the bending and reducing points should be slow, and the elbows and reducing pipes should be as few as possible, especially the elbows that transition from horizontal to vertical should be less. The inner wall of the tube should be smooth, no wrinkles or bulges, and no grid-like components are installed.
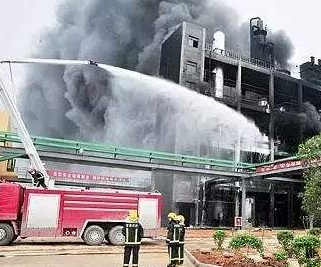
The welding quality of the pipeline meets the requirements, and the welding seam must be inspected by non-destructive testing. The connection method of the pipeline is reasonable, and the installation errors such as section deviation, gap, misalignment or non-concentricity can be eliminated by adding offset pads or multi-layer pads. When pipes pass through walls, floors and roofs, casings, fire shoulders, waterproof caps and other devices should be added. Welds, flanges and other joints should avoid walls and floors. Pipes and pipe fittings should not be in direct contact with pipe racks, and should be isolated by adding wooden pads, soft metal sheets or rubber asbestos pads according to the design temperature and pressure requirements.
、
3. Take anti-corrosion measures
Select corrosion-resistant materials according to the corrosiveness of the conveyed materials. For example, for the corrosion of hydrogen sulfide, chromium steel, stainless steel or aluminized steel can be used at different temperatures; Cr-Mo alloy steel is used for hydrogen embrittlement under high temperature conditions; In order to prevent high temperature oxidation corrosion, use austenitic stainless steel pipe, 5Cr or 9Cr steel pipe.
Take reasonable anti-corrosion measures, such as coating anti-corrosion, lining anti-corrosion, electrochemical anti-corrosion, and using corrosion inhibitor for anti-corrosion. Among them, coating anti-corrosion is widely used, and in coating anti-corrosion, coating anti-corrosion is used the most.
Regularly check the corrosion of the pipeline, especially the pipeline network system laid underground, and repair or replace the severely corroded parts in time.
4. Eliminate residual stress of pipeline
In order to avoid pipeline vibration, measures such as setting up vibration damping devices and increasing flexible design can be taken.
In order to weaken the destructive effect of thermal stress, a thermal compensation method that increases the flexibility of the piping system and relieves the thermal stress is adopted, such as using a special thermal compensator; using a spring hanger structure or a stopper to constrain the displacement of the pipeline in the constraining direction, Set up a fixed bracket near the nozzle of the equipment to weaken the stress and moment of the nozzle, add elbows, change the direction of the pipeline, increase the overall flexibility of the piping system, or use methods such as thermal insulation.
To take measures for different external loads, such as preventing the foundation from sinking, you can adopt the method of changing the location of the pipeline or the support method or strengthening the foundation design; to prevent the impact of external force, you can strengthen the protective facilities, flexible design, reasonable setting, adding guardrails or casing and methods to strengthen construction supervision.
5. Strict safety operation
During the production operation, the process parameters such as the conveying temperature, pressure and flow rate of the materials should be controlled strictly according to the process requirements, especially the pipelines used for conveying combustible gas, combustible liquid and combustible powder and granular materials, the conveying speed should not be higher than the technological value. The key parts of production, such as heating furnace mouth, tower bottom, reactor bottom, high temperature pump and other inlet and outlet pipelines and pipelines with harsh working conditions and pipelines subject to alternating loads, should pay special attention.
The delivery pipeline of cooling medium should ensure the supply of cooling medium and avoid interruption. If necessary, two-way water source and power control can be installed to prevent the vicious circle of over-temperature and over-pressure in the production system.
Remove dirt, sediment and other sediments in the pipeline in time, and it is strictly forbidden to use iron tools or appliances that can generate sparks to transport unstable sediments that are flammable, explosive, and spontaneously flammable. Regularly remove dust from pipes and surrounding equipment and facilities to reduce dust deposition.
Before and after the freezing season, pay attention to the antifreeze and thawing of the pipeline, such as the water trap, the elbow of the pressure gauge, the condensate valve, etc., and take thermal insulation and antifreeze measures in time when problems are found. For temporarily unused water or pipelines that are easy to freeze, the medium in the pipe should be drained.
Repair the pipeline in time, and strictly prohibit overload, overdue and sick operation.
6. Strengthen fire safety management
The pipelines in use shall be regularly inspected in accordance with the "Regulations on Safety Management and Supervision of Pressure Pipelines" to detect leakage and damage to the pipelines to prevent leakage and leakage in the pipeline system.
The exhaust replacement of the pipeline should be carried out according to the regulations before parking for maintenance and start-up. When conducting hot maintenance work, all rules and regulations for hot work must be strictly followed.
It is strictly forbidden to stack flammable and explosive substances around dangerous material pipelines and high temperature pipelines. It is strictly forbidden to stack all kinds of sundries on the pipelines that need heat dissipation to prevent the accumulation of heat and cause fires.
Avoid various sources of ignition around the hazardous material conveying pipeline.
7. Take anti-static measures
The conveying pipeline for powder and granular materials should be made of materials with good electrical conductivity, and a static elimination device with good performance should be installed. Oxygen pipelines, acetylene pipelines, oil storage and transportation equipment, ventilation devices, and air pipelines in factories and workshops must be connected and grounded. Anti-static grounding devices should be installed every 100m at the beginning, end, branch and straight sections of pipelines laid on the ground or in trenches. The grounding resistance should not be greater than 30Ω.
8. Set up fire and explosion-proof safety devices
Explosion-proof pressure relief devices such as safety valves should be installed on pipelines prone to overpressure explosion; water seals, sand seals, flame arresters or fire dampers should be installed on pipelines prone to flame spread. Check valves and shut-off valves should be installed at the junctions between high-pressure and low-pressure systems and on pipelines that are prone to backflow. Install pipeline filters at the inlets of pumps and valves to prevent accidents caused by impurities or inclusions.
Conveying pipelines with fire and explosion hazard should be equipped with inert medium pipeline protection. The exhaust gas discharge pipeline of combustible gas should be sealed with nitrogen gas or equipped with flame arrester and other devices to prevent the spread of fire. The dense pipe network system with high fire risk can be equipped with a flammable gas concentration detection and alarm device to detect hidden fire hazards in time, and water sprinkler and other fire-extinguishing facilities can also be set up to fight the initial fire in time.