When designing the RTO electrical system, the company will consider a variety of safety explosion-proof, and is well aware of the importance of explosion-proof in the fine chemical industry, so the editor of Ausiyi Environmental Protection Engineering will talk about how to do safety and explosion-proof from simple to deep.
First of all, we need to be clear, under what circumstances will an explosion occur? First of all, explosive combustion requires three elements: combustibles, combustion-supporting materials, and ignition sources, all of which are indispensable.
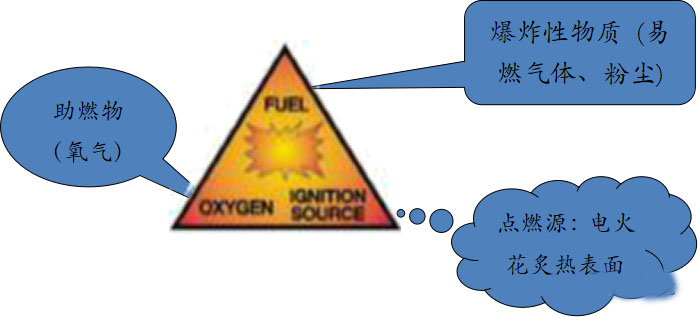
How to prevent explosions, we need to start from these three fundamental conditions, namely: 1. Avoid the formation of an explosive environment; 2. Try to eliminate possible ignition sources; 3. If explosions are inevitable, try to minimize losses. However, in the waste gas treatment industry, VOCs treatment equipment is basically used in dangerous places, and the media recovered by the VOCs treatment device are also flammable and explosive dangerous gases, so they have the conditions for potential combustion and explosion. In response to such a situation, we can only set up barriers to the predicted risk factors to prevent the occurrence of ignition sources (sparks and high temperature), and the measures taken are to take explosion-proof safety measures for the electrical equipment and non-electric equipment (moving equipment) of the VOCs treatment system.
Definition of explosion-proof equipment: electrical equipment that will not cause ignition of the surrounding explosive atmosphere under specified conditions.
Determining factors of explosion protection class
1. In order to determine the application scope of explosion-proof electrical equipment, explosion-proof equipment is divided into three categories:
Class I: electrical equipment underground in coal mines;
Class II: electrical equipment for all other explosive gas atmospheres except coal mines and underground;
Class III: Electrical equipment in explosive dust atmospheres other than coal mines.
2. According to the different types of gases, Class II is further divided into:
A (typical gas: propane), B (typical gas: ethylene), C (typical gas: hydrogen)
3. Electrical equipment for explosive environments is divided into T1~T6 groups according to the highest surface temperature:
T1:450℃;T2:300℃;T3:200℃;T4:135℃;T5:100℃;T6:85℃;
Maximum surface temperature: The highest temperature reached by any part of the electrical equipment that may cause ignition of the surrounding explosive atmosphere when the electrical equipment is operated under the most unfavorable operating conditions within the specified range. The maximum surface temperature should be below the flammable temperature.
4. According to the different explosion-proof technology selected in different application places, the commonly used explosion-proof equipment is divided into:
Flameproof type, positive pressure type, potting type, oil-filled type, sand-filled type, increased safety type, intrinsically safe type, non-sparking type, etc.
So how do we blast off?
1. Explosion-proof type-EX D
Design based on standards: GB3836.1-2000, GB3836.2-2000
Flameproof electrical equipment: Electrical equipment with a flameproof enclosure.
Flameproof enclosure: It should be able to withstand the explosion pressure of the internal explosive gas mixture and prevent the internal explosion from spreading to the surrounding explosive mixture. (Zone 1 explosion-proof technology)
Principle: Dangerous gas is allowed to enter the flameproof enclosure, and explosion may occur in the enclosure. However, it is required that the shell must have sufficient strength; and each shell joint surface must have a sufficiently long meshing length and a sufficiently small gap to ensure that the internal explosion will not pass through the flameproof joint surface and cause the external environment to explode. The flameproof joint refers to the joint where the opposite surfaces of the various components of the flameproof casing are matched together in order to prevent the internal explosion from spreading to the explosive gas mixture around the casing.
Features: It is a gap explosion-proof technology, which relies on the gap and meshing length to achieve the effect of cooling/extinguishing.
Strength design: at least 1.5 times the reference pressure, usually IIB/1MPa, IIC/1.5MPa.
2. Increased safety type-EX e
Design based on standards: GB3836.1-2000, GB3836.3-2000
Increased safety electrical equipment: a type of equipment that does not produce arcs, sparks or may ignite explosive mixtures under normal operating conditions, and further measures are taken to improve its safety and prevent the possibility of dangerous temperatures, arcs, and sparks. of electrical equipment.
The increased safety type is a zone 1 explosion-proof technology. "e" is the first letter of "enhanced".
Principle: The equipment is required to be free from sparks, arcs and dangerous temperatures under normal operation and approved overload conditions.
Increased safety technology is a German technology. In principle, it can be applied to Zone 1 sites, but the degree of international or inter-industry recognition is slightly different. The increased safety enclosure is not required to have the strength to withstand internal explosions, but at least it should be able to withstand the specified mechanical shock and have an enclosure protection level of IP54.
Secondly, technical measures such as terminal loosening prevention, reliable structural connection, current-carrying limitation, winding insulation, temperature protection, electrical clearance/creepage distance, etc. must be taken.
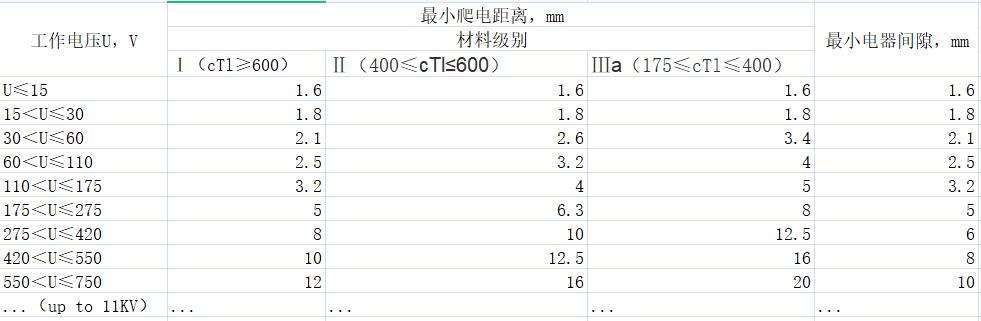
For general-purpose junction boxes, in addition to meeting the enclosure strength, protection class, electrical clearance and creepage distance, the maximum allowable power dissipation must be determined through tests, and ensure that it does not exceed the allowable temperature of enclosure materials, insulating parts, and temperature groups.
Typical applications: In addition to junction boxes, there are also electromagnetic coils (valves), lighting fixtures, transformers and brushless motors. Automatic instruments usually have potentiometers or selector switches for zero/full scale adjustment, that is, sparks are considered to be generated under normal circumstances, so they are generally not designed as Exe.
3. Intrinsically Safe-EX i
Design based on standards: GB3836.1-2000, GB3836.4-2000
Intrinsically safe electrical equipment: refers to electrical equipment in which all internal circuits are intrinsically safe circuits, that is, any spark or any thermal effect generated by the circuit under the conditions specified in the standard (including normal operation and specified fault conditions) cannot be ignited Circuits specified for explosive gas atmospheres.
Intrinsically safe as zone 0 (ia)/zone 1 (ib) explosion-proof technology. "i" is the first letter of "intrinsic safety"
Features: It is a "safety design" technology that suppresses the energy of the ignition source as an explosion-proof method. It is required that the electrical spark and thermal effect that the equipment may produce under normal working and fault conditions are less than the minimum ignition energy and self-ignition temperature of the explosive dangerous gas, respectively. For example, H2, 19uJ, 560°C.
Intrinsically safe technology is actually a low power design technology. Therefore, it is well suited for industrial process automation instruments.
Basic design technical measures (circuit and structural design aspects)
- limit voltage;
- limit current;
- limiting energy (including energy storage elements: capacitors and inductors);
- Reasonable selection of component rating parameters, current-carrying conductor cross-section, etc.;
- Structural and circuit separation measures.
Technical and commercial characteristics of intrinsically safe explosion protection
- Simple manufacturing process, small size, light weight and low cost (switch circuit 1:4);
- It is easy to realize the design of higher explosion protection level;
- It can be operated and maintained with power on;
- High safety and reliability;
- Can effectively avoid electric shock casualties;
- Wide range of applications;
- Simple equipment only needs to meet the general requirements and can be connected to the intrinsically safe explosion-proof system without certification.
Type of electrical equipment
1. Intrinsically safe equipment - electrical equipment in which all internal circuits are intrinsically safe circuits;
2. Intrinsically safe related equipment – electrical equipment equipped with intrinsically safe circuits and non-intrinsically safe circuits, and the structure is such that the non-intrinsically safe circuits cannot adversely affect the intrinsically safe circuits. (Associated equipment is generally installed in a safe place)
Class of intrinsically safe equipment
1. Exia – electrical equipment that cannot ignite explosive gas mixtures during normal operation, one fault and two faults. Intrinsically safe equipment can be installed in Zone 0, Zone 1, Zone 2 hazardous locations. Intrinsically safe related equipment can be connected to Zone 0, Zone 1, Zone 2 hazardous locations. Exia is zone 0 explosion-proof technology;
2. Exib - Electrical equipment that cannot ignite explosive gas mixtures in normal operation and in the event of a malfunction. Intrinsically safe equipment can be installed in Zone 1 and Zone 2 hazardous locations. Intrinsically safe related equipment can be connected to Zone 1 and Zone 2 hazardous locations.
When designing the explosion-proof performance of the exhaust gas treatment system, it is necessary to determine the level of the dangerous area that may explode according to the explosive environment on site, and select the matching explosion-proof electrical equipment according to the different dangerous area levels to avoid the occurrence of safety accidents and ensure the entire exhaust gas treatment system. Safe, stable and smooth operation.